Manufacturing and Production: Bringing Innovations to Life
Designing the Future: Innovation in Product Development
Product development represents a critical phase in manufacturing, encompassing the complete product lifecycle from initial concept to final delivery. Cross-functional teams comprising engineers, designers, and marketing professionals collaborate to transform consumer needs into tangible solutions. Market awareness and consumer insight form the foundation for developing products that meet evolving demands and achieve commercial success. This stage requires rigorous research, iterative testing, and continuous refinement to ensure products meet quality standards and fulfill their intended purposes.
The design process progresses from conceptual sketches to detailed 3D models and functional prototypes. Effective teamwork and communication prove vital for overcoming design challenges and optimizing product features. This developmental phase fundamentally influences manufacturing efficiency and ultimately determines market reception. Professionals in this field benefit greatly from strong visualization skills and innovative thinking.
Optimizing Production Processes: Efficiency and Quality
Process optimization stands as a cornerstone of competitive manufacturing, balancing efficiency gains with cost containment. Modern facilities implement advanced solutions including automated systems, robotic technologies, and comprehensive quality control protocols. Data analytics play an increasingly important role in identifying improvement opportunities and implementing corrective measures.
Strategic inventory control, supply chain optimization, and resource allocation contribute significantly to operational smoothness and cost efficiency. Waste reduction strategies coupled with output maximization techniques enhance both profitability and market competitiveness. Contemporary manufacturing increasingly incorporates Lean principles to achieve these operational objectives.
Quality Control and Assurance: Maintaining Standards
Consistent quality maintenance forms the bedrock of brand reputation and customer satisfaction. Rigorous quality control protocols, including multi-stage testing and inspection procedures, identify and correct production anomalies. This proactive quality approach prevents costly defects and ensures product reliability throughout the usage lifecycle.
Implementation of recognized quality assurance frameworks, such as ISO certification programs, builds trust with customers and business partners. These systems verify compliance with industry standards and best practices. Comprehensive documentation of quality processes supports continuous improvement initiatives and facilitates problem resolution.
Supply Chain Management: Connecting the Dots
Effective supply chain management ensures seamless material flow throughout production cycles. This complex function includes raw material procurement, logistics coordination, and supplier relationship management to prevent disruptions. Expertise in global trade regulations, international shipping protocols, and customs procedures proves essential in today's interconnected markets.
Risk management strategies address potential disruptions from geopolitical events, market fluctuations, and supply chain vulnerabilities. Successful mitigation of these risks ensures production continuity and reliable product availability. This dynamic field requires constant adaptation to evolving market conditions and emerging technologies.
IoT sensor networks revolutionize data collection, enabling real-time monitoring of diverse physical parameters. This continuous data stream provides critical insights into environmental conditions, equipment performance, and various other metrics. Instantaneous data access facilitates predictive maintenance and process optimization. This real-time analytical capability supports informed decision-making and preemptive issue resolution.
Marketing and Sales: Connecting Innovation with the World
Connecting Innovation with Global Markets
Successful marketing and sales strategies effectively bridge innovative solutions with worldwide markets. This requires in-depth research to understand varying consumer preferences across cultural contexts. Identifying optimal communication channels involves expertise in digital marketing, social media trends, and international business practices. Cultural sensitivity and adaptability prove crucial when tailoring campaigns for maximum global impact.
Localization of marketing materials requires careful attention to linguistic nuances, cultural values, and regional customs to ensure appropriate messaging. Monitoring global economic trends and shifting consumer behaviors enables ongoing strategy refinement. This dynamic approach ensures continued relevance in an ever-changing marketplace.
Building Strong Brand Identities
Compelling brand development transcends visual identity, creating meaningful narratives that resonate with target audiences. This process requires deep consumer insight and the ability to articulate product value propositions clearly across multiple platforms. A cohesive brand message maintains consistency while adapting to diverse cultural contexts.
Marketing collateral—from digital platforms to print materials—must reflect this brand essence while maintaining flexibility for different markets. Successful brands balance core identity preservation with cultural adaptation to achieve global recognition.
Developing Effective Sales Strategies
Strategic sales approaches drive revenue growth and business objectives. Understanding complete sales cycles enables targeted approaches for different customer segments. Relationship-building, exceptional service, and effective objection handling foster customer loyalty. Market awareness and adaptability distinguish successful sales professionals in competitive environments.
Managing and Motivating Teams
Effective team leadership fosters collaborative, productive work environments. Clear communication and well-defined expectations align team efforts with organizational goals. Recognizing individual strengths, providing constructive feedback, and strategic task delegation optimize team performance.
Analyzing Data and Measuring Results
Data-driven decision-making enhances marketing and sales effectiveness. Tracking key performance indicators—including digital engagement metrics and conversion rates—informs strategy adjustments. Market trend analysis enables proactive strategy refinement for improved targeting and results. Comprehensive analytics evaluate campaign ROI and guide continuous improvement initiatives.
Regulatory Affairs and Compliance: Ensuring Safety and Efficacy
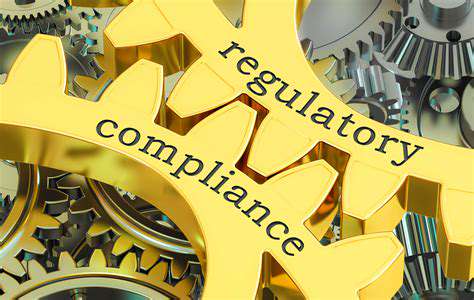
Essential Regulatory Compliance Procedures
Regulatory compliance represents a critical function for organizations in regulated industries. Comprehensive regulatory knowledge coupled with procedural adherence minimizes legal risks and maintains stakeholder trust. Continuous monitoring of regulatory changes enables timely process adjustments to maintain compliance. Non-compliance consequences include significant penalties, reputational harm, and operational disruptions. Meticulous compliance documentation provides audit trails and demonstrates commitment to standards.
Effective compliance programs incorporate multiple elements: clear policies, staff training, and robust monitoring systems. Regular internal audits and external assessments identify improvement opportunities and verify ongoing compliance. Proactive compliance management reduces risks while optimizing operational efficiency.
Maintaining Documentation and Records
Comprehensive record-keeping demonstrates regulatory adherence. This includes documenting approvals, modifications, and procedural deviations. Organized document management systems facilitate efficient retrieval during audits or inquiries. Secure systems with version control and access restrictions ensure document integrity.
Documentation should encompass all operational aspects from development through distribution. Regulatory correspondence records also provide valuable reference material. Well-maintained documentation supports compliance while serving as an organizational knowledge resource.
Internal Controls and Audits
Robust internal controls prevent errors and ensure regulatory adherence. These safeguards should promote accuracy and prevent violations. Ongoing control monitoring significantly reduces non-compliance risks. Regular internal audits evaluate control effectiveness and identify enhancement opportunities.
Audit scope should cover all relevant operations including development, manufacturing, and distribution. Qualified auditors should conduct thorough examinations with detailed findings analysis. Comprehensive audit documentation supports compliance verification and improvement initiatives.