Protein engineering breakthroughs now allow scientists to redesign enzyme structures at the molecular level. By strategically replacing key amino acids or adding stabilizing domains, we can create robust variants that withstand harsh processing conditions while maintaining full catalytic activity.
Exploring Novel Enzyme Sources
The search for novel enzymes has expanded to Earth's most extreme environments. Hydrothermal vents, polar ice caps, and hypersaline lakes harbor extremophiles producing enzymes that function where conventional proteins would instantly denature.
Recent metagenomic studies of unculturable microbial communities reveal an astonishing diversity of previously unknown enzymes. These discoveries continuously expand our biocatalytic toolbox, enabling reactions once considered impossible under mild conditions.
Engineering Enzyme Specificity
Tailoring enzymes for specific industrial needs represents one of biotechnology's most exciting frontiers. Modern techniques combine computational modeling with advanced laboratory evolution:
Cutting-edge directed evolution platforms can now generate and screen millions of enzyme variants in days, accelerating the discovery of catalysts with precisely tuned properties. This revolution has already yielded commercial enzymes with 1000-fold improved activity for key industrial processes.
Developing Multi-Enzyme Systems
Nature rarely relies on single enzymes - complex metabolic pathways employ coordinated enzyme teams. Scientists now mimic this strategy by designing synthetic enzyme cascades that perform multi-step syntheses in single reactors.
Optimizing Reaction Conditions
Maximizing biocatalytic efficiency requires meticulous reaction engineering. Beyond basic parameters like pH and temperature, modern optimization considers:
Advanced kinetic modeling now enables real-time adjustment of reaction parameters to maintain optimal enzyme performance throughout entire production runs. This precision control can double or triple product yields compared to traditional batch processing.
Integrating Biocatalysts into Industrial Processes
The final hurdle involves scaling laboratory successes to industrial production. Key challenges include:
Innovative immobilization techniques now allow enzyme reuse for hundreds of cycles, dramatically improving process economics. Continuous flow bioreactors represent another breakthrough, enabling 24/7 production with minimal downtime.
Bio-Based Materials for Sustainable Energy Storage and Transmission
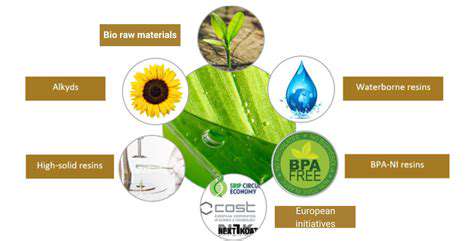
Bio-Based Materials: A Sustainable Revolution
The materials revolution is quietly transforming global manufacturing. Where petroleum once dominated, we now see remarkable alternatives emerging from nature's laboratory - cellulose nanofibers stronger than steel, algae-based bioplastics, and fungal mycelium packaging materials.
The environmental calculus is compelling: bio-based materials typically generate 60-80% fewer greenhouse emissions across their lifecycle compared to petroleum counterparts. Perhaps more importantly, they offer a pathway to break our civilization's dangerous dependence on finite fossil resources.
Exploring Diverse Bio-Based Sources
The search for optimal feedstocks considers multiple factors:
Agricultural byproducts like rice husks and sugarcane bagasse solve two problems simultaneously - creating valuable materials while reducing farm waste. Meanwhile, fast-growing bamboo and hemp offer renewable alternatives to slow-growth timber.
Properties and Applications of Bio-Based Plastics
Modern bioplastics have shattered previous performance limitations:
Polylactic acid (PLA) now matches PET in clarity and rigidity for packaging, while polyhydroxyalkanoates (PHAs) offer marine-degradable alternatives for single-use items. The most advanced variants even outperform conventional plastics in moisture barrier properties - a crucial breakthrough for food packaging.
Manufacturing Processes and Sustainability
Green chemistry principles guide next-generation production:
Novel enzymatic processing methods reduce energy needs by up to 70% compared to traditional petrochemical routes. Closed-loop systems recover and reuse nearly all solvents and catalysts, minimizing waste.
Economic Viability and Market Growth
The economic landscape is shifting rapidly:
As production scales up, bioplastic prices have fallen 40% in five years, now competing directly with conventional plastics in many applications. Government mandates in the EU and Asia are accelerating adoption, with global markets projected to triple by 2030.
Challenges and Future Directions
Key research frontiers include:
Improving thermal stability remains crucial for automotive and electronics applications. Perhaps most importantly, we need standardized composting infrastructure to realize the full environmental promise of biodegradable variants.
Environmental Impact and Lifecycle Assessment
Comprehensive LCAs reveal nuanced realities:
While bio-based materials generally show clear environmental advantages, optimal outcomes require regionally appropriate feedstocks and energy-efficient production. The most sustainable solutions often combine bio-based materials with smart design for minimal material use and maximal recyclability.